|
Полевые АЭ Испытания днищ РВС АННОТАЦИЯ Методика испытания с помощью акустической эмиссии (АЭ) на коррозию и утечки плоских днищ наземных резервуаров-хранилищ нефтепродуктов при атмосферном давлении была разработана в рамках проекта, финансируемого Еврокомиссией. Распознавание изображений, основанное на частотных областях, использовалось для идентификации механизма обнаруженных источников АЭ, расположенных на днище резервуара. Изложены основы примененного метода и методики испыта-ния, а также приводятся результаты выполненных испытаний вместе со статистическими результата-ми классификации испытанных днищ резервуаров. Обычный неразрушающий контроль днищ резервуаров в основном опирается на осмотр и измерение толщины стенок и потому отражает прошлые периоды технического обслуживания всего резервуара. С другой стороны, АЭ позволяет следить за активными процессами, происходящими во время испытаний в днище резервуара при условиях, аналогичных нормальным условиям эксплуатации резервуара. Сочетание того и другого приводит к комплексной оценке состояния днища резервуара, воспользовавшись преимуществами обоих подходов: определение общей степени ухудшения качества днища резервуара и слежение за фактическими процессами снижения качества, происходящими при данных условиях эксплуатации.
ВВЕДЕНИЕ
С тех пор, как данная методика испытания была выведена на рынок средств технического обслужи-вания и проверки, было проверено более чем 200 резервуаров на нефтеочистительных заводах, химических производствах и нефтехранилищах. Результаты, полученные с помощью других методов НК, сравнивались с результатами АЭ испытаний. Для того чтобы иметь возможность сочетать информацию о разных НК технологиях, необходимо точное знание условий проведения всех меро-приятий по техническому обслуживанию (как текущих, так и предыдущих) и всех подготовительных работ к очистке резервуара для внутреннего обследования. По сравнению с АЭ испытанием, которое занимает резервуар с содержащимся в нем нефтепродуктом всего лишь на один-два дня, внутреннее обследование приводит к простою резервуара в течение недель, а то и месяцев. Это подчеркивает увеличение полезного времени использования резервуара и преимущество АЭ испытаний РВС на коррозию и утечки.
Во многих странах продолжительность периодов до следующего внутреннего обследования ограни-чена несколькими годами. Тогда резервуар должен быть выведен из работы, и очень часто внутрен-нее обследование проводится только для того, чтобы еще раз подтвердить хорошее состояние внут-реннего днища. Многие владельцы резервуаров, которые очень хорошо знают их общее состояние по задокументированным результатам технического обслуживания, все еще подвергают эту методику сомнениям. Ухудшение состояния внутреннего днища из-за коррозии, особенно общей коррозии, можно довольно действенно предотвратить за счет проведения соответствующих мероприятий, например, нанесения внутреннего покрытия или катодной защиты. Поэтому, если условия эксплуата-ции не выходят за известные пределы безопасных мероприятий, качество днища резервуара не долж-но серьезно ухудшиться. Но все-таки могут возникнуть непредвиденные ситуации, которые приведут к более агрессивным видам коррозии с более высокой скоростью, чем ожидается. Это может произойти в тех местах на внутреннем днище резервуара, где внутреннее покрытие было повреждено, или из-за загрязнения хранящегося продукта коррозионно-активными веществами, скапливающимися на дне. Тогда ограниченные временем интервалы внутреннего обследования могут лишь случайно выявить возникновение коррозии. Что более вероятно, они могут лишь засвидетельствовать имеющееся коррозионное разрушение, чтобы отремонтировать затронутые им части днища.
Акустико-эмиссионное испытание, напротив, позволяет определить резервуары с активными коррозионными процессами, при этом, не вмешиваясь в их эксплуатацию. Поэтому АЭ является действенным инструментом технического обслуживания и проверки, помогающим владельцу резервуара вовремя предотвратить серьезный ущерб. Оптимальные условия для такого мониторинга создаются, когда его начинают при возвращении резервуара в эксплуатацию после внутреннего обследования. В этом случае текущее состояние днища резервуара, как правило, точно определяется с помощью проверки днища, поэтому ранее измерение посредством АЭ дает идеальную точку отсчета для повторяющихся испытаний в будущем. Информация о протекании процессов в резервуа-ре накапливается таким образом, что может быть использована в существенном удлинении периодов технического обслуживания вплоть до следующего мероприятия с вмешательством в его эксплуата-цию. Стоимость подготовки резервуара к внутреннему обследованию может легко достичь 100 тысяч евро, поэтому за счет применения АЭ можно добиться существенной экономии.
МЕТОДИКА ПРОВЕДЕНИЯ ИСПЫТАНИЯ
Источники расходов, связанных с коррозией РВС, многочисленны, и экономические издержки от нее, очевидно, огромны. Кроме прямых расходов важную роль играют и косвенные, например, из-за простоя предприятия или потери продукта. Представленная методика испытания позволяет определить и локализовать активные коррозионные процессы на днище резервуара и в случае, когда они уже проникли в днище, обнаружить и локализовать утечку. Поэтому она является полезным средством технического обслуживания, позволяющим более экономично бороться с разрушением днищ резервуаров. В общем, акустическая эмиссия ограничена обнаружением активных дефектов. Но это ограничение оборачивается преимуществом, поскольку этот метод неразрушающего испытания (НК) выявляет только те дефекты, которые оказывают воздействие на разрушение днища резервуара (прогрессирующее утончение стенки) или на безопасность резервуара (фактические потери продукта). Рис. 1 показывает типичный пример РВС для сырой нефти. 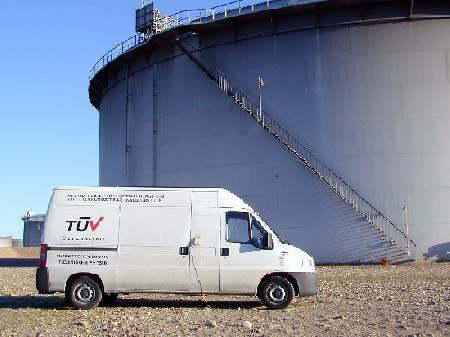
Рекомендованная максимальная продолжительность следующего периода до обслуживания определяется в зависимости от эксплуатационных условий во время испытания. И ответственному лицу на месте однозначно сообщается, что условия, устанавливаемые владельцем резервуара для подготовки последнего к испытанию, должны быть как можно ближе к обычным условиям эксплуатации. То есть, если условия эксплуатации остаются такими, какими они были перед испытанием, то это дает возможность сделать прогноз состояния днища. Отсюда следует, что после изменения условий эксплуатации классификация состояния днища резервуара теряет смысл, и необходимо провести повторное испытание, чтобы оценить новые условия. Если днищу резервуара присвоена IV степень, рекомендуется провести внутреннее обследование для подтверждения данных, выявленных при АЭ. Работы по подготовке к АЭ начинаются с определения характеристик резервуара (подробности конструкции, содержащийся продукт и т.п.). Для этой цели мы обычно посылаем вопросник вместе с базовой информацией о нашей методике испытания. После проверки заполненных документов ответственного контактного лица на месте необходимо распределить все необходимые ресурсы. Наш персонал сертифицирован для АЭ по стандарту EN 473 и использует сочетания современных измери-тельных систем AMSY-5 компании Vallen-System. Рис 2 показывает систему, собранную в фургоне, который находится рядом с резервуаром. .jpg)
Перед каждым испытанием необходимо однозначно сообщить ответственному представителю заказчика, что на каждое АЭ измерение оказывает влияние шум различного происхождения (механи-ческий, электрический и т.д.). Бóльшая часть шумовой информации может быть опознана с помощью программ и, таким образом, отфильтрована так, что не сможет исказить результат испытания. Но важнее всего при подготовке резервуара на месте просто избегать шума, чтобы он не был воспринят АЭ датчиками. Если перед испытанием были приняты соответствующие меры, например, устранены источники шума или процесс перенесен на менее шумное время, то шумовая составляющая уже будет ограничена низким уровнем, и алгоритмы подавления шумов не придется усиливать до предела. Тем самым повысится надежность результатов испытания, что очень важно, особенно, если впоследствии будет рекомендовано провести затратные мероприятия. Стандартная схема требует располагать АЭ датчики, как минимум, через каждые 15 м вдоль периметра РВС и на высоте примерно 1 м. Нижний ряд датчиков позволяет локализовать АЭ события, в пределах горизонтального сечения резервуара (2-я локализация). Рассматриваемая траектория прохождения звука (см. рис. 3) от источника на внутреннем днище резервуара до датчика АЭ на ее корпусе проходит через жидкий штатный продукт, поэтому при локализации используется скорость звука в нем. Такая схема подходит в том случае, когда можно исключить события, вызвав-шие АЭ, не на днище, а в других частях (например, в плавающей крыше). В любом другом случае мы настоятельно рекомендуем располагать датчики в два ряда. С помощью этих дополнительных датчиков на высоте примерно 3 – 5 м над днищем и в точности над датчиками около него, предостав-ляется возможность исключать из оценки АЭ события из более верхних зон резервуара дополнитель-но и повышать надежность оценки состояния днища. Пример АЭ датчиков, установленных на корпу-се резервуара, можно видеть на рис. 3 слева. 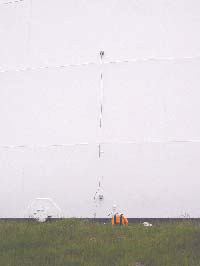 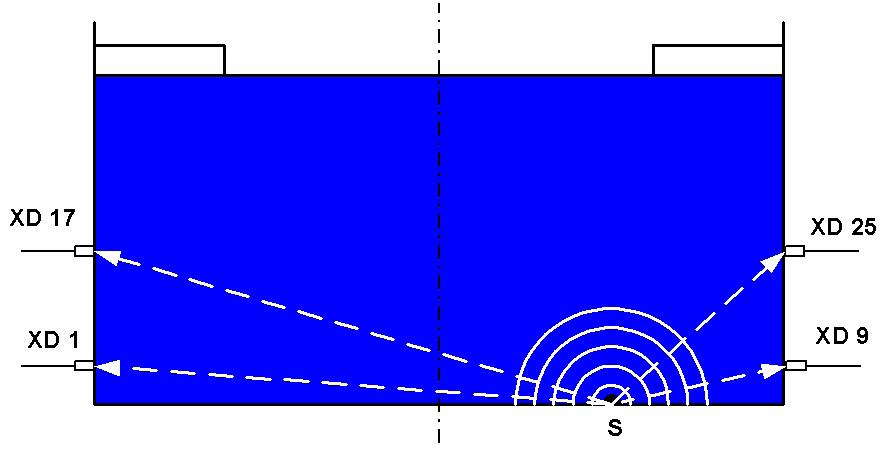
Как только зафиксирован источник АЭ на днище резервуара, важно определить механизм источника, чтобы правильно оценить состояние днища. Определение механизма источника фактически включает в себя три следующих аспекта:
1. сбор и предварительная обработка данных, 2. представление данных и 3. принятие решения,
которое ведет к разработке системы распознавания образов. При выборе наилучшего способа представления данных следует учитывать, что площадь днища резервуара может достигать 1000 квадратных метров. Поэтому расстояние от источника на внутреннем днище до датчика на корпусе резервуара может меняться в широком диапазоне, а с ним и параметры АЭ сигнала, например, максимальная амплитуда сигнала, его длительность и энергия, соответственно. Применяемая методика испытания использует те формы сигнала, которые получаются и сохраняются параллельно с другими параметрами АЭ сигнала. По данным формы волны можно рассчитать частотную характеристику звуковых волн и использовать для представления данных. Рис. 4 показывает типичную форму АЭ сигнала с его частотной характеристикой. Прохождение звуковой волны в жидкостях свободно от частотной дисперсии, в связи с чем частотная характеристика не зависит от расстояния между источником и датчиком. Более того, затухание интересующей полосы частот около 30 кГц, может считаться равномерным. Отсюда следует, что частотная характеристика АЭ сигнала не зависит от расстояния между источником и АЭ датчиком. Классификатор был разработан с помощью базы опорных данных, включающих формы волн сигналов с хорошо известными механизмами источников. Этот инструмент затем применялся к неизвестным данным для того, чтобы решить, с чем связан обнаруженный источник АЭ — с коррозией или утечкой. Если механизм источника ока-жется утечкой, это значит, что днище резервуара относится к «степени IV», в связи с чем рекоменду-ется как можно скорее открыть резервуар. При обнаружении коррозии результат может различаться от «степени II» до «степени IV» в зависимости от активности источника. Более того, во втором шаге классификации обнаруженный источник коррозии приписывается либо к прочно укоренившейся коррозии, на которую указывает присутствие слоя продукта коррозии, либо к началу коррозии, когда слой ржавчины только начинает развиваться. В том случае, когда никакой активности не обнаружено, резервуар не имеет каких-либо активных дефектов и поэтому с точки зрения АЭ может эксплуатиро-ваться еще пять лет без дополнительного технического обслуживания. 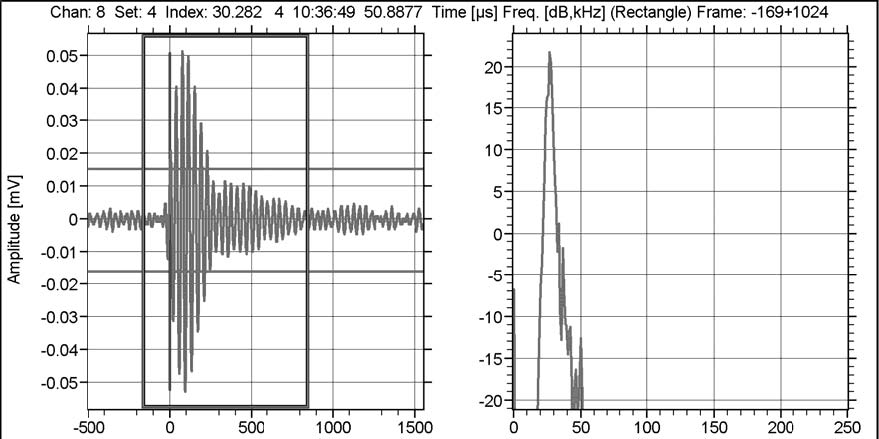
СТАТИСТИКА ПРОВЕДЕННЫХ ИСПЫТАНИЙ За годы, прошедшие после введения описанной методики испытания на рынок услуг технического обслуживания и проверки, было испытано более 200 резервуаров, в основном, в Германии, Австрии и Италии. Диапазон диаметров испытанных РВС (с фиксированной или плавающей крышей) — от 4,5 м (резервуар для продукции химического предприятия) до 98 м (резервуар для сырой нефти храни-лища на нефтепроводе). Штатный продукт находился при температуре окружающего воздуха, а также при повышенных температурах (80 °C — максимальная температура поверхности в месте нахождения датчика) с термоизоляцией корпуса резервуара или без нее. Рис. 5 показывает распреде-ление по штатным продуктам, сгруппированным в три основные категории. Такие дистилляты, как нафта, бензин, газойль или жидкое топливо отнесены к «продуктам переработки нефти», тогда как химикаты, например, ацетон, трихлорэтилен, пропиленоксид, а также каустическая сода были добав-лены в категорию «продукты». 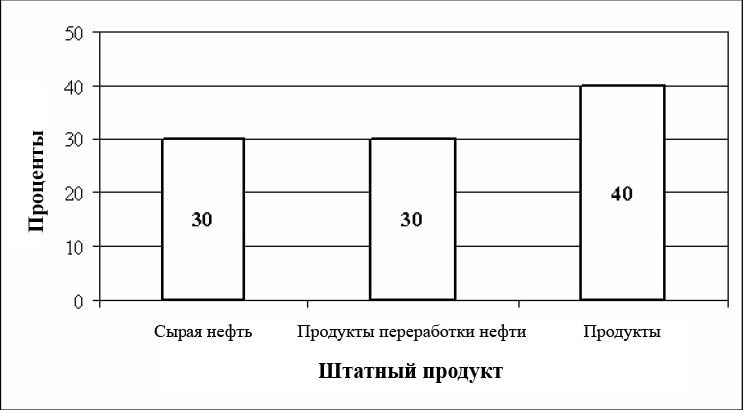
В общем, возможности применения испытательной методики охватывают широкий диапазон штатных продуктов, используемых в различных отраслях промышленности, а соответствующие РВС были успешно испытаны с помощью АЭ. Рис. 6 показывает распределение результатов испытания в соответствии с четырьмя степенями из таблицы 1. По этому распределению можно понять, что большинство резервуаров (52%) были отнесены к «степени I», свидетельствующей о наилучшем состоянии днища. Это подчеркивает важность опыта многих владельцев резервуаров в том, что регулярные внутренние проверки ведут к затратным открытиям резервуаров, находящихся в хорошем состоянии. Введение АЭ в регулярную программу технического обслуживания и проверки позволяет определять те резервуары, у которых период обслуживания может быть продлен на несколько лет безопасной эксплуатации до следующей внутренней проверки. 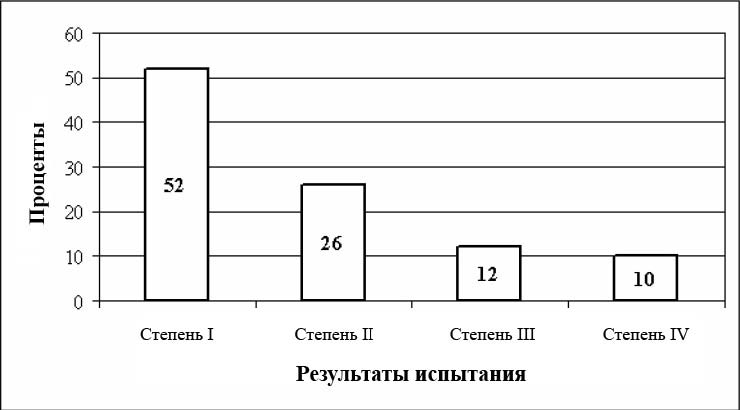
Надежность нашей методики испытаний была подтверждена дважды: безопасной эксплуатацией резервуаров в течение рекомендованного периода между техническими обслуживаниями и многими последующими проверками. Поскольку результатом АЭ является вывод, касающийся активных дефектов при условиях проведения испытания, он дополняет результат внутренней проверки, целью которой является оценка общего снижения качества днища резервуара. Это следует помнить при сравнении обоих видов испытания. По сравнению с результатом АЭ при вынесении окончательной оценки состояния днища необходимо иметь подробные сведения об истории технического обслуживания резервуара, а также принять во внимание мероприятия, проводившиеся для ее очистки. В качестве примера мы провели эксперимент в одном случае, когда в процессе очистки было удалено внутреннее покрытие из-за его недостаточного сцепления с поверхностью в той зоне, где уже было установлено наличие коррозионного повреждения. Поскольку состояние днища резервуара было отнесено к «степени I», на первый взгляд казалось, что этот дефект не был замечен. После изучения истории эксплуатации резервуара был обнаружен хорошо задокументированный факт, что внутрен-нее покрытие наносилось на данное коррозионное повреждение после дробеструйной обработки, но без ремонта. В конце концов, оказалось, что результат АЭ был правильным и представлял фактиче-ское состояние днища, имевшееся после процедуры очистки резервуара. Конечно, результат внутрен-ней проверки тоже был правильным, фактически показав общее ухудшение состояния днища резер-вуара. Этот случай должен лишь подчеркнуть, что благотворное сочетание обоих результатов иногда требует точного знания истории эксплуатации резервуара и мероприятий при подготовке входа в резервуар. В большинстве случаев мы наблюдали, что такое подробное рассмотрение не проводилось из-за согласованности результатов: днище резервуара в хорошем состоянии. Согласно рис. 6, был испытан ряд РВС в достаточно плохом состоянии. Были найдены днища резер-вуаров с сильной общей коррозией, а также днища с локализованными формами коррозии и резер-вуара с утечками. Как уже можно было предположить, на другом конце системы классификации степеней до принятия дальнейших действий тоже нужно было прояснить некоторые признаки. Так как метод АЭ способен обнаружить активную коррозию, он также обнаруживает в резервуаре протекторные аноды. Вместе с владельцем резервуара мы можем определить, что найденные призна-ки коррозии находятся там, где были помещены протекторные аноды. В другом месте серьезный источник коррозии обнаружился не на днище резервуара, а на плавающей крыше. При использовании двухрядного расположения датчиков, показанного на рис. 3, можно уверенно определить нахождение источника коррозии на плавающей крыше. Там она уже проникла в сварочный шов, а на листах обшивки был найден продукт. Коррозия плавающей крыши идентифицируется АЭ и тем самым ухуд-шает качество классификации днища и даже не дает правильно ее выполнить. С помощью двух рядов датчиков все это можно сделать достаточно просто и эффективно. В целом, каждая идентификация серьезного дефекта вначале анализируется на предмет других возможных причин во избежание затратных ложных вызовов. Рис. 7 показывает оба вида оценки для примера с коррозией крышки: без помощи датчиков второго ряда и с ними. Горизонтальный разрез резервуара показан в плоскости x-y вместе с расположениями датчиков и идентификациями нижнего ряда, в то время как в вертикальном направлении приводится количество событий, локализованных АЭ, в эталонной зоне в час. Легко можно увидеть, что опознавание (красная колонка слева) исчезает в результате преимуществ улуч-шенного расположения датчиков (справа). 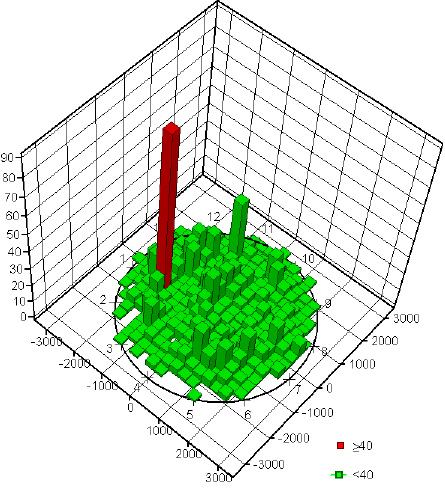 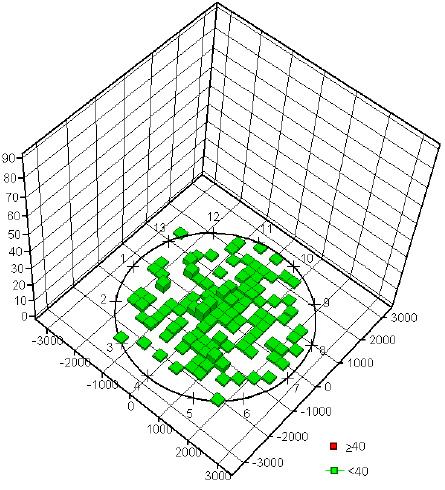
ВЫВОДЫ
Испытания днища резервуаров с помощью акустической эмиссии (АЭ) способно обнаружить актив-ную коррозию (прогрессирующее утонение стенки) и активную протечку (фактическую потерю про-дукта). Это испытание охватывает 100% днища резервуара, а также нижнюю и верхнюю стороны листов пола. Будучи интегрировано в программу регулярного технического обслуживания и обследо-вания, оно является важным инструментом отделения резервуаров в хорошем состоянии, способных выдержать еще несколько лет безопасной эксплуатации, от резервуаров в плохом состоянии, которые необходимо открыть для внутреннего обследования и ремонта. Применение представленной методики испытания позволяет открывать резервуары тогда, когда того требует состояние днища, а не при наступлении предписанных графиком сроков. Таким образом, техническое обслуживание может быть сосредоточено на тех резервуарах, в которых обнаружены признаки сильного повреждения.
Правила эксплуатации резервуаров во всех европейских странах неодинаковы. Имеются разные огра-ничения на длительность периода технического обслуживания до следующего внутреннего обследо-вания. Для получения официального одобрения увеличения периода технического обслуживания владельцу резервуара нужно убедить ответственные власти, что уже привело к первым успешным результатам.
|